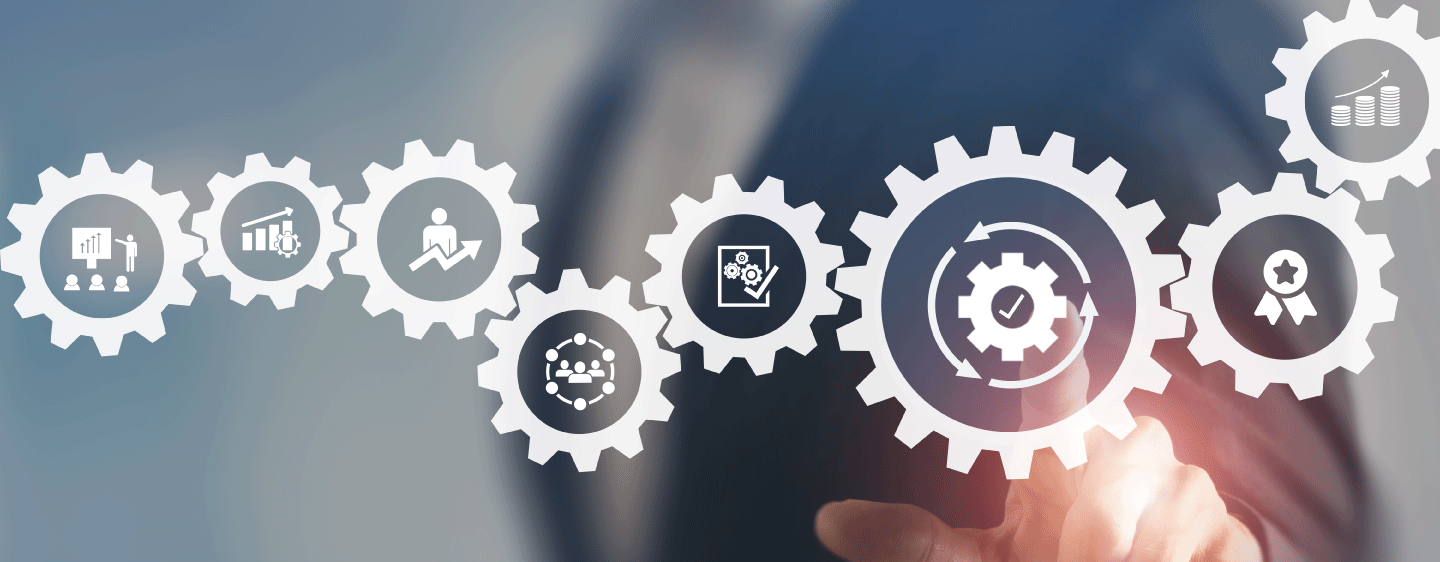
Torque and Tensioning
Hydraulic Torque and Tensioning
Controlled bolting is an essential process in industries that demand high precision and safety during assembly, such as the oil and gas sector, power generation facilities, and various manufacturing environments. In these industries, the reliability and safety of operations heavily depend on the proper assembly of components, where even a minor error can lead to significant consequences. Properly tightened bolts are crucial for ensuring the integrity and performance of bolted connections, as they help maintain the structural stability and functionality of equipment. This is especially important in high-stress environments like flanged joints, pressure vessels, and piping systems, where the forces and pressures involved can be immense. In such settings, any failure in the bolted connections can lead to leaks, equipment damage, or even catastrophic failures, underscoring the importance of controlled bolting techniques to maintain operational safety and efficiency.
This introduction will delve into the basic principles of controlled bolting, concentrating on the two primary methods employed in flange management: torquing and tensioning. Grasping the essential differences, benefits, and drawbacks of each method is crucial for choosing the appropriate techniques.
Torque vs. Tension
Hydraulic Torque Wrenches
-
How it works: Torquing is a mechanical process that involves applying a specific rotational force, known as torque, to a bolt or fastener to achieve the desired tension and secure it in place. This process is crucial in ensuring that the bolt is tightened to the correct specifications, which is essential for the integrity and safety of the assembly. The technique utilizes a torque wrench, a specialized tool designed to apply a precise amount of torque, allowing the user to tighten bolts to a predetermined torque level. This ensures that the bolts are neither too loose, which could lead to structural failure, nor too tight, which could cause damage to the bolt or the components being joined. Operators can achieve consistent and accurate results using a torque wrench, which is vital in applications where precision and reliability are paramount.
- Widely accessible: Torque wrenches are not only relatively inexpensive, making them a cost-effective choice for both professional and personal use, but they are also designed to be user-friendly. This ease of use means that individuals with varying experience levels can operate them effectively, reducing the need for extensive training or technical expertise. Their affordability and simplicity make them a popular tool in many settings, from commercial to extensive industrial facilities.
- Quick application: Torque wrenches are particularly advantageous in scenarios where time is of the essence. Their design allows for rapid application, as they do not require any specialized equipment beyond the wrench itself. This makes them ideal for tasks requiring swift completion, such as emergency repairs or maintenance work, where minimizing downtime is crucial. The straightforward nature of the tool ensures that users can quickly achieve the desired torque without unnecessary delays.
- Commonly used: Torque wrenches have become a staple in various industries due to their reliability and effectiveness. They are well-established tools that have been integrated into numerous sectors, including automotive, construction, and manufacturing. Their widespread use is a testament to their versatility and dependability, as they are often employed for general bolting applications. This commonality ensures that they are readily available and that users can easily find support and resources.
- Less precision: Torque readings can be significantly influenced by various factors such as friction between the bolt and the surface it is being tightened against, the presence of surface coatings that can alter the frictional characteristics, or even the elongation of the bolt itself during the tightening process. These variables can introduce discrepancies in the actual torque applied versus the intended torque, potentially leading to an inaccurate clamping force. This inaccuracy can compromise the integrity of the assembly, as the bolt may not be tightened to the precise specifications required for optimal performance and safety. In critical applications, such as those found in aerospace or high-pressure systems, even minor deviations in torque can have serious consequences, making it essential to account for these factors during the torquing process.
- Risk of uneven load: While effective in many scenarios, the torque method may only sometimes ensure a uniform load distribution across all bolts in an assembly. This uneven distribution can be particularly problematic in applications where precise load balance is crucial, such as in flange management or when securing components that must maintain a specific alignment under stress. In such cases, the uneven application of torque can lead to stress concentrations, which may cause premature wear, deformation, or even failure of the components involved. Ensuring an even load distribution is vital to maintaining the structural integrity and longevity of the assembly, necessitating additional measures or alternative methods to achieve the desired outcome.
- Hydraulic Pump (10,000 psi/700 bar operating pressure)
- Hydraulic Torque Wrench (High-Cycle or Low Clearance)
- Torque Wrench Accessories such as reaction arms, reaction pads or flow control valves
- Torque Wrench Hoses
- Couplers
- Gauge
- Oil
Tension vs. Torque
Hydraulic Tensioning
-
How it works: Tensioning uses a hydraulic tool to elongate the bolt and exert a direct axial force, reaching the required clamping load. This approach generally provides greater accuracy in maintaining consistent tension across all bolts.
- Precise load control: Hydraulic tensioning allows for the direct measurement of bolt tension, significantly enhancing the accuracy and reliability of the results. By precisely controlling the load applied to each bolt, this method ensures that the desired tension is achieved without guesswork, reducing the likelihood of errors that can occur with indirect measurement techniques. This precision is crucial in applications where maintaining exact specifications is vital for the integrity and safety of the assembly.
- Even load distribution: Hydraulic tensioning is critical in ensuring a more uniform load distribution across all bolts, which is particularly important in applications involving critical flanges. By applying a consistent axial force to each bolt, the tensioning process minimizes the risk of uneven stress, which can lead to potential failures or leaks in the system. This uniformity is essential in maintaining the structural integrity and performance of the assembly, especially in high-pressure or high-temperature environments where even minor discrepancies can have significant consequences.
- Reduced risk of over-tightening: One key advantage of hydraulic tensioning is the reduced risk of over-tightening, as the tension is measured directly rather than estimated. This direct measurement allows operators to apply the exact amount of force needed, preventing the application of excessive load that can damage the bolts or the components they secure. By avoiding over-tightening, the longevity and reliability of the assembly are enhanced, reducing the likelihood of maintenance issues or failures that could arise from compromised bolt integrity.
- More complex: The hydraulic tensioning process is inherently more complicated due to the necessity of specialized tools and equipment, such as hydraulic bolt tensioners, which are designed to apply precise force to the bolts. This complexity arises from ensuring that each component is correctly calibrated and maintained to function effectively. Additionally, the setup and operation of these tools require a thorough understanding of the system, which can add layers of complexity to the process.
- Higher cost: The financial investment in hydraulic tensioning is typically higher because the tools involved, such as tensioners and pumps, are more expensive than standard torque wrenches. Furthermore, using these tools often necessitates hiring trained technicians with the expertise to operate them safely and efficiently. This requirement for skilled labor can further increase the overall cost, as it involves the initial purchase of equipment and ongoing training and maintenance expenses.
- Slower: The hydraulic tensioning process can be slower than traditional torquing methods, mainly when dealing with larger assemblies or complex flanged connections. Each bolt must be individually tensioned to ensure uniform load distribution, which can be time-consuming. The meticulous nature of the process, combined with the need for precise adjustments and checks, contributes to a longer duration, especially in scenarios where accuracy and reliability are paramount.
- Tensioning Pump (21,750 psi/1,500 bar)
- Tensioners
- Tensioning hoses
- Couplers
- Gauges
- Oil
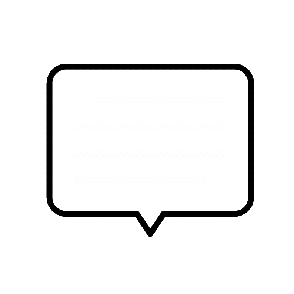
Connect with Our Team
Complete the form and a member of our team will get back to you shortly.

Solution Development

Technical Expertise

Accurate Estimates

On-site Support

Regulatory Guidance
- 1
- 2